Commercial scale composting
With the club’s enthusiastic use of composting, members might be interested in how professional businesses go about this operation compared to our own smaller personal efforts. The following describes the official opening of a brand new facility on the Tablelands in Far North Queensland. The Federal Member for the area did the honours and cut the ribbon, and the local Council Mayor and Councillors from several surrounding shires were present for the occasion. Apologies should be given up front for some of the pictures being somewhat blurry as many were taken through the window of the bus that took attendees round for a tour of the large site.
We’re all aware that local governments round the world are wrestling with expanding municipal waste disposal problems and that historical landfill practices are increasingly seen as unsustainable. Composting of the organic component of these wastes is being actively explored as a solution that also has immense positive benefits regarding soil degradation/fertility, erosion and leaching. The owner of this new facility had been an orchardist/farmer in the area who was bitten by the composting bug and after improving his soil and crop yields over a 10 year period he became so committed he decided to sell up and go full-time with a commercial composting business. The goal was to sell product primarily to local orchardists and farmers but also councils endeavouring to improve parks and gardens, schools and sporting clubs wanting grassed fields that could be played on, mining companies who have to rehabilitate sites, and government road works where extensive topsoil may have been removed or lost and vegetation had to be re-established on slopes to prevent future erosion and re-create some natural beauty in the area. With the compost at his orchard he’d improved his soil organic matter content from 2 to 9% over that 10 year period, and for example his banana plants became so healthy with enormous bunches; individual fruit became so large they were above the normal supermarket specifications for contractual supply. And this sort of improvement was done on the Tablelands where the red volcanic soil is just so much better than our WA coastal sands before you do anything.
He’s invested millions in this venture and the prospects are that he’s going to make a roaring success of it.
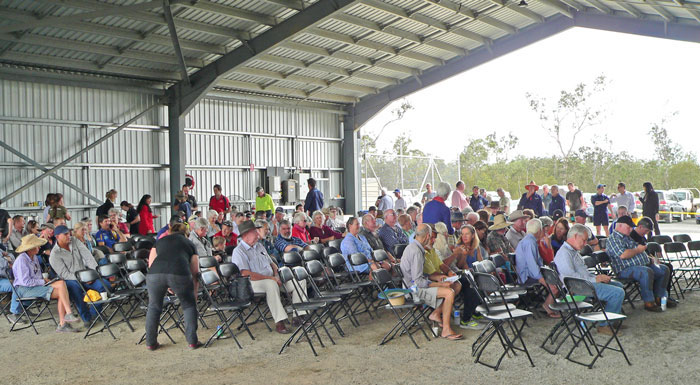
His first forays into the business involved visiting several facilities around Australia and then in the US and Europe to bring back ideas for creating a state-of-the-art facility. Two consultants were contracted to guide the whole development, one a soil scientist very experienced in delivering these programs around Australia and who could assist in satisfying the regulatory hoops and paper-work for government approval and certification, and the other a PhD level horticulturalist specialising in plant nutrition. Both have been continuously involved in the development of the business from the outset, and they gave talks during the launch explaining the principles involved, process management, desired outcomes and the specific effects on soils and crops that can be attained.
After selecting a block of suitable size and location, he cleared an initial 20 Ha for start-up. He then managed to obtain economically-priced uncontaminated feedstock from the Cairns Council – about half of all their green waste is trucked up to the Tablelands after being shredded. It’s a continuous operation for a specially designed semi-trailer which has a movable belt floor such that on arrival at site, the load is pushed out the back end without any other machinery involved. This together with shredded wood comprises the total solid compost input materials. There is a special shredder with accompanying feeder crane shown in one of the pictures that can handle all wood off-cuts (treated wood is not accepted) from the building trade, saw mills etc. This machine is quite impressive as in quiet times it’s also used to shred car and truck tyres for outside clients, including steel-belted types where the steel and any fabric is separated from the rubber. In the picture the wood chips come out on the conveyor belt and the rest through a separate chute. Water is the only other item that goes into the compost mix (ie no manures or other starter components, acidity regulating agents etc).
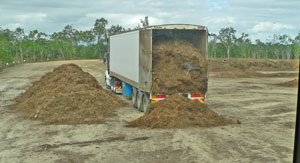
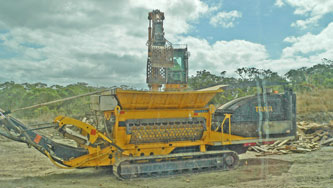
The feedstock is then arranged in long windrows 5-6m high and 6-8m wide. It takes about 35 truck-loads of feed to build up one of these.
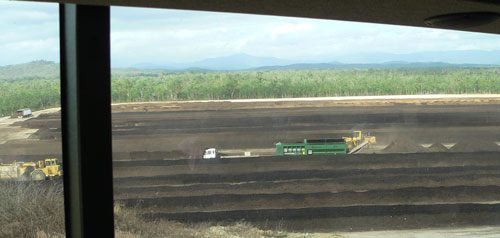
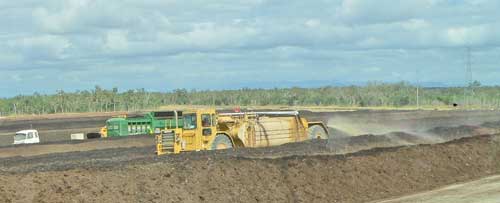
By launch day he’d built up 30,000 tonnes of compost at various stages of maturity, and depending on market demand he has the logistics in place to greatly expand the amount of stock on site. In the picture showing several windrows you can see a green screener, where mature compost that’s ready for sale goes through a particular size screen depending on client specifications and intended use. Larger wood stock pieces not yet broken down sufficiently to pass through the screen are separated and then added back into younger windrows for subsequent breakdown.
After establishing the windrows,the material has to be moistened to about 60%. This can’t be done all in one stage as much of the water would simply pass through as run-off. So several passes with a large capacity water truck must be made to ensure water soaks in properly. Water supply is from a naturally-sourced run-off dam that he’s custom built on site. The material goes through the normal hot composting process of an initial rapid build-up in temperature to a maximum of about 65oC when it’s then turned by a special machine that moves along, straddling the windrow. The base mechanics involves a large horizontal spinning drum with projecting paddles (like a waterwheel); each of these pick up portions of mix which is then rotated to the back and sprayed out behind the machine. About 1000 tonnes/hr can be turned(!), on a scale hard to imagine with what we can manage fork in hand on our own mulch bins. One downside of all this heavy machine capability of course is the fuel required, and he kept quoting diesel consumption figures required for this operation and others as we went round – very necessary to ensure the venture remains economically viable. In one of the pictures, as material from the core is turned over you can see plumes of steam venting from the internally-generated heat of the pile. Windrow temperature is measured a number of times/wk in this initial phase and when this falls below 60oC it’s turned again. This continues, with appropriate watering, until the thermophilic stage is completed in the first 20-30 days or so. The rate of turning in the cooler maturing stage can then slow down, with fully mature compost being ready after about 130 days.
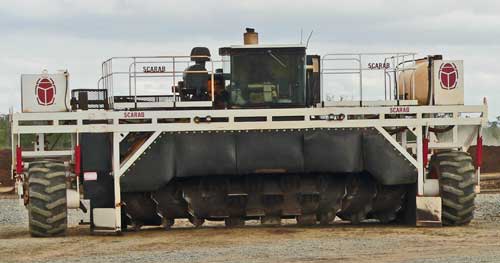
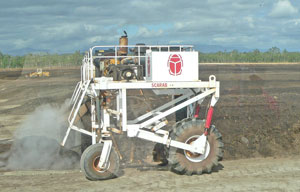
Depending on circumstances, windrows might be turned up to 20 times. Since all composting is out in the open and the region is on the edge of a tropical rainforest, undue heavy and sustained rainfall can alter intended moisture content. However it takes about 500mm of continuous rain before the desired aerobic conditions are severely compromised and the windrow goes anaerobic and smelly. This is not usual but when it does happen the windrows are not lost or need to be removed. When the rain stops the mix can all be dried out again by frequent turning until it gets back down to the desired moisture range. To satisfy Australian standards and accreditation requirements, final product is monitored to ensure it’s compliant ie free of a number of pathogens (eg Pythium, Salmonella etc), pesticides, viable weeds and industrial chemicals, and that any toxic heavy metals are below regulated levels.
After this it’s ready for sale. NPK in the final product averages about 16, 7.2 and 14kg/tonne, with a common application rate of 5-6 tonne/Ha. This can be given a number of times a year, particularly with nutrient hungry species or when soil fertility is low. The slow release properties of compost mean that gentle fertilisation of soils is achieved with minimal loss through leaching or vaporisation. In the owner’s previous world as a banana grower he found he could more than halve his chemical fertiliser input and still achieve superior outcomes. With their turner they can easily mix through lime or other materials requested by clients before delivery depending on what they prefer for their soil conditions. They can also supply a service that spreads the compost on farm/orchard sites. This is a large truck that has a special horizontal disc wheel at the back. Compost is fed down onto this spinning wheel at a suitable rate and by centrifugal action it’s spun off horizontally onto the soil either side. With a throw of 4m on each side, truck passes for covering a field can be 8m apart unless overlap is wanted. Use of the spreader was demonstrated and its effectiveness in terms of application speed could easily be appreciated.
The owner and the consultants emphasised throughout that the quality of municipal feedstock was paramount (ie no glass, metal, plastics, rubber, industrial waste chemicals etc), and also that frequent temperature monitoring is essential in ensuring windrow conditions are kept at optimal levels of aeration and moisture, ie how often you need to turn/spray for total elimination of pathogens and rapid breakdown of materials to finish with properly mature compost that’s ready to go straight on the ground without soil nutrient drawdown or other negative effects. They also emphasised that no-till is perfectly effective in providing nutrients to crop plants as most feeder roots are in the top 10cm or so. Indeed with established perennial fruit trees no-till is often the only option. They reminded all that as organic matter continually breaks down you have to continue to add new material each year. If you’re starting with very low levels then don’t expect a quick fix as it might take several years to increase to effective levels.
Listening and talking to growers at the end of the day, the whole promotion effort seemed effective in convincing many of them to explore using compost on their properties if they weren’t already doing so. And this is saying something given as a group they can be very hard to move from established practices, particularly where large monetary sums are involved. Maybe all of this could inspire you to have a go with your own effort. You could do a lot worse than supplying lots of this ‘black gold’ to your babies, and they’ll love you for it.